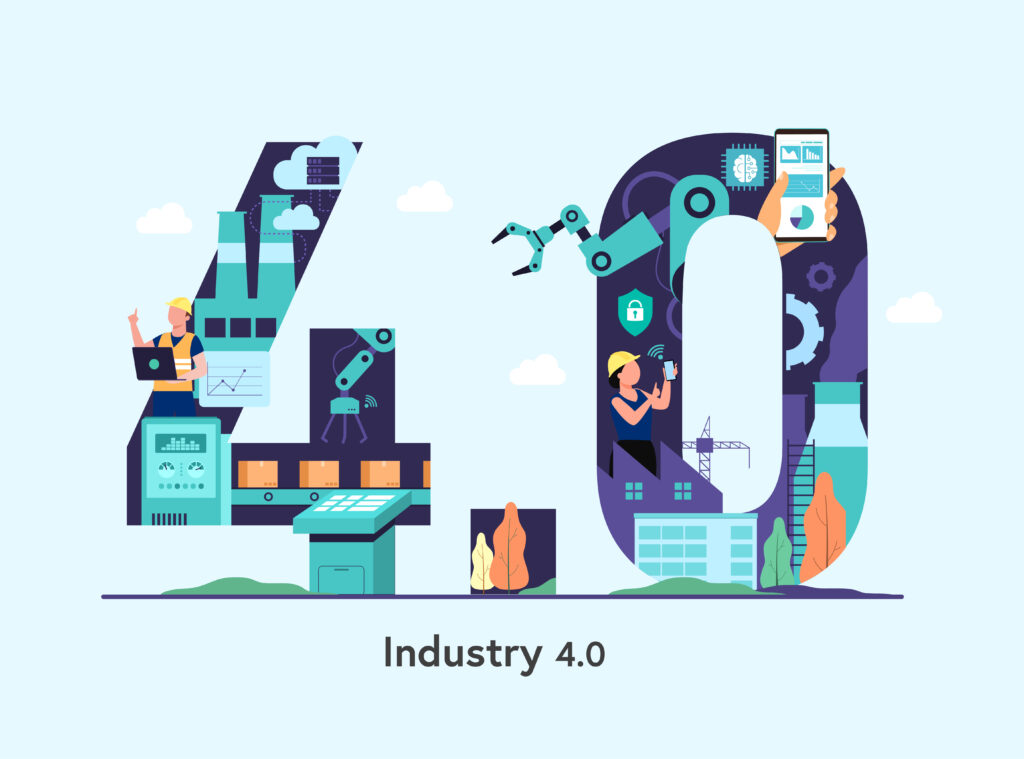
Industry 4.0, also known as the Fourth Industrial Revolution, represents an unprecedented transformation in the manufacturing and industrial sectors. This technological revolution is not just an evolution but fundamentally reinvents how businesses design, produce, and operate. It is characterized by the intelligent integration of cutting-edge technologies, the creation of ultra-fast communication networks, and the exploitation of artificial intelligence. Industry 4.0 emerges as a powerful catalyst that is redefining the future of production worldwide.
Origins
Where does the term « Industry 4.0 » come from? The term « Industry 4.0 » originated in Germany in 2011 during the Hannover Fair, a major international event dedicated to industry. The « 4.0 » concept refers to the fourth industrial revolution, following mechanization, electrification, and automation. Industry 4.0 signifies the industry’s entry into the digital and interconnected era, marked by automation and robotics.
This industrial revolution is a result of the evolution of major industries that have shaped the history of production. It involves key industries that played a crucial role in the creation of Industry 4.0.
First Industrial Revolution – Mechanization The First Industrial Revolution began when machines started being powered by steam engines. Prior to this, most products were made by hand. With machines, production became faster and more efficient as they could perform tasks more quickly than humans. This shift from artisanal methods to factory production transformed how objects were made.
Second Industrial Revolution – Electricity The Second Industrial Revolution was marked by the advent of electricity. Factories began using electricity to power their machines. This had a tremendous impact as electric machines were more flexible and efficient than steam-powered ones. Result: factories could operate for longer periods and produce more.
Third Industrial Revolution – Automation and Computerization The Third Industrial Revolution saw the rise of automation. Machines could perform much work without human intervention. This period also saw the introduction of computers in factories, which were used to control and supervise industrial operations, making production even faster and more precise.
Fourth Industrial Revolution – Blending Worlds The Fourth Industrial Revolution, or Industry 4.0, represents a major milestone. It merges the physical (machines and real objects), digital (computers and software), and biological (humans) worlds. This revolution employs advanced digital technologies to make production smarter. Machines can make decisions on their own and adapt to changes. It’s as if machines and computers are constantly learning and improving to produce higher-quality products more efficiently.
Definition of Industry 4.0
Industry 4.0 is a major transformation in the world of production. Factories and businesses now use new technologies such as computers, artificial intelligence, and machines to produce products faster and better than before. It’s like machines talking to each other to work more intelligently. In other words, Industry 4.0 involves the integration of cyber-physical systems into production and logistics processes. This integration is achieved through automation, robotics, artificial intelligence, digital manufacturing, and the Internet of Things (IoT). These technologies enable the creation of smart factories where machines and systems can self-organize.
In Industry 4.0, there is an increase in interconnection and communication among machines, systems, and products. This interconnection is made possible through IoT and big data technologies, allowing for greater flexibility, increased efficiency, and improved production quality. Industry 4.0 represents a significant evolution in how products are manufactured and delivered, offering new opportunities for businesses across all sectors. However, it also presents challenges, including data security, privacy concerns, and workforce skills.
Technological Foundations of Industry 4.0
1. Internet of Things (IoT) IoT is a central pillar of Industry 4.0. It involves the interconnection of objects, machines, and systems via sensors and networks. This extensive connectivity allows real-time data collection from the production environment, including information on temperature, pressure, location, machine status, and more. IoT enables companies to monitor their assets and processes in real-time, improving decision-making, predictive maintenance, and operational efficiency.
2. Big Data and Data Analytics Big Data refers to the management and analysis of vast amounts of information. In Industry 4.0, companies collect extensive data from diverse sources, including IoT, sensors, production systems, and databases. Analyzing this data helps extract valuable insights, detect trends, and reveal correlations. These insights help businesses optimize operations, forecast equipment failures, improve product quality, and make informed decisions.
3. Artificial Intelligence (AI) and Machine Learning AI is a key technology driving automation and efficiency in Industry 4.0. It allows machines and systems to make informed decisions and learn from data. Machine learning, a branch of AI, is particularly important as it enables machines to improve over time and adapt their behaviors based on collected information. In Industry 4.0, AI is used for tasks such as predictive maintenance, production optimization, defect detection, and more.
4. Cyber-Physical Systems (CPS) CPS represents the fusion of the physical and digital worlds, where computing systems closely interact with physical processes. CPS integrates sensors, actuators, embedded systems, and communication networks to monitor, control, and optimize production processes. This close interconnection enhances responsiveness, optimizes energy efficiency, and supports real-time data-driven decision-making.
5. 5G Connectivity 5G ultra-fast connectivity is crucial for Industry 4.0. It ensures instant communication between devices, machines, and systems. 5G enables real-time data exchanges, paving the way for advanced applications such as telemedicine, augmented reality, autonomous vehicles, and more. This rapid connectivity enhances coordination, monitoring, and responsiveness in the industrial environment.
6. Cloud Computing Cloud Computing provides essential infrastructure for managing storage, processing, and analyzing big data. It allows companies to store vast amounts of data generated by sensors and IoT devices, which is crucial for advanced data analytics at the heart of Industry 4.0. Cloud computing supports real-time data analysis, offering valuable insights from raw data quickly. AI and machine learning models are often executed in the cloud, enabling machines to become smarter over time. This technology also fosters rapid and efficient connectivity, allowing machines, systems, and individuals to access data and applications in real-time, enhancing communication and coordination in production.
Challenges and Concerns
1. Data Security and Privacy One major concern of Industry 4.0 is data security. With the proliferation of connected devices and real-time data collection, companies face the need to protect sensitive information. Cybersecurity threats are becoming increasingly sophisticated, and companies must implement robust defense mechanisms to prevent data breaches. Data privacy is also a concern, as ensuring that sensitive information is not exposed to unauthorized parties is crucial.
2. Workforce Adaptation The introduction of advanced technologies, such as automation and AI, requires a workforce capable of leveraging them effectively. This involves training employees and developing new skills. Adapting workers to a constantly evolving production environment is a key challenge. Investing in training and support is essential to ensure employees can work harmoniously with new technologies.
3. Infrastructure Upgrades Industry 4.0 relies on cutting-edge systems, but many companies still have outdated infrastructure. Upgrading equipment, networks, and systems is costly and complex. Companies must address the capital investment needed to modernize their infrastructure. Additionally, transitioning to Industry 4.0-compatible infrastructure may disrupt ongoing operations, making change management crucial.
4. Ethical Considerations The technological advances of Industry 4.0 raise significant ethical questions. Issues such as AI decision-making, privacy concerns for workers and consumers, and social and environmental implications require thorough consideration. Companies must engage in ethical and responsible practices to address these challenges. This involves considering the impact of their actions on society, the environment, and the workforce, and implementing ethical policies and procedures to guide their conduct.
Characteristics of a Smart Factory
A smart factory is at the forefront of Industry 4.0. It integrates advanced technologies to achieve high levels of automation, efficiency, and flexibility. Key characteristics include:
1. Advanced Automation A smart factory relies on advanced automation of production processes. Operations are carried out by cyber-physical systems, minimizing human intervention for repetitive tasks. Robots, autonomous machines, and automated transport systems contribute to smooth production.
2. Connectivity and IoT IoT is at the heart of a smart factory. Machines, equipment, and products are equipped with sensors and communication devices, allowing tight connectivity. Data is collected in real-time for continuous monitoring and advanced analytics.
3. Data Management and Big Data A smart factory generates vast amounts of data. Effective data management, combined with big data analytics, enables informed decision-making. Data is used to improve quality, preventive maintenance, and overall efficiency.
4. Flexibility and Customization The smart factory is designed for flexible production. It can quickly switch from one product series to another without extended downtime. Customizing products based on customer needs is also facilitated.
5. Sustainability and Ecology Smart factories integrate sustainable production practices. They minimize waste, optimize resource use, and reduce carbon footprints. Energy efficiency and the use of renewable energy sources are priorities.
6. Responsiveness and Adaptability The smart factory is responsive to market changes and fluctuations. It can quickly adapt to new requirements, product developments, and customer demands.
7. Predictive Maintenance Equipment in the smart factory is continuously monitored, allowing for predictive maintenance. Failures are anticipated, and maintenance is performed at optimal times to avoid costly downtimes.
8. Security and Privacy Data and operational security are paramount. Smart factories implement robust security measures to protect systems and information against cybersecurity threats.
Why is Industry 4.0 Important for My Business?
Industry 4.0 is crucial for your business because it helps you stay competitive in an increasingly digital world. It enables you to optimize production processes, reduce costs, enhance product quality, and drive innovation. Additionally, it improves your ability to understand and meet customer needs more effectively. Moreover, Industry 4.0 can attract and retain top talent, as many professionals are drawn to companies that leverage cutting-edge technologies.
The Benefits of Industry 4.0
Industry 4.0 offers numerous substantial benefits that are transforming how businesses operate and thrive:
- Enhanced Operational Efficiency
Advanced digital technologies, such as process automation, optimize operations and reduce production costs. - Flexibility and Adaptability
Cyber-physical systems and 5G connectivity provide great flexibility, enabling businesses to quickly adapt to market changes, customer demands, and new opportunities. - Improved Quality
The use of sensors and AI to monitor and control production ensures consistent, high-quality products. - Faster Time-to-Market
Automated processes and instant communication speed up product development and market launch. - Increased Personalization
Data collected through IoT and Big Data allows for customized products and services tailored to individual customer needs. - Environmental Sustainability
Resource optimization, waste reduction, and real-time monitoring contribute to more environmentally friendly production. - Better Supply Chain Visibility
Industry 4.0 enhances tracking of materials, products, and processes throughout the supply chain, improving logistical management. - New Business Models
Increased connectivity supports the development of new business models, such as connected services. - Increased Security
Advanced cybersecurity systems protect industrial operations from online threats, enhancing overall security. - Creation of New Jobs
While automation may eliminate some roles, Industry 4.0 also creates new opportunities, particularly in technology sectors.
In summary, Industry 4.0 provides significant advantages in efficiency, innovation, sustainability, and competitiveness for businesses that embrace these advanced technologies. It redefines how we design, manufacture, and deliver products, paving the way for new opportunities and sustainable growth.
Leave a Reply